Inventory shrinkage happens when your merchandise gets damaged or goes missing in a warehouse or in transit. While some shrinkage is an inevitable part of doing business, there are plenty of ways that you can control and minimize the amount of shrinkage you face.
Weโll quickly cover what shrinkage is, what can cause it, and how to calculate it so you can tell if your level of shrinkage is improving or not. Then, weโll get into how the right technology and the right partnerships can safeguard your business against inventory shrinkage.
What Is Inventory Shrinkage?
Inventory shrinkage is the loss of inventory that occurs when the recorded stock levels in a company’s system do not match the actual physical inventory. This can result from theft, damage, administrative errors, or supplier fraud. Shrinkage impacts profitability and operational efficiency, which makes it an essential metric for businesses to track, while actively finding means to prevent it.
The Causes of Inventory Shrinkage and the Latest Trends
However, inventory shrinkage can lead to backorders, longer delivery times, and ultimately unhappy customers. According to the National Retail Federation, the average shrink rate is up to 1.6%, amounting to $112.1 billion in losses across the fiscal year.
Not even large retailers are immune to the effects of inventory shrinkage, with Home Depot reporting an 8-basis-point reduction in gross profit margin year over year due to inventory shrinkage. In order to address this growing problem among retailers and brands of all sizes, itโs key to first identify the primary causes, including:
- Theft โ Both employee theft in the warehouse or retail stores, and shoplifting in brick-and-mortar stores contribute to inventory loss, making security measures crucial.
- Administrative Errors โ Mistakes in data entry, pricing, labeling, or inventory tracking can create discrepancies.
- Supplier Fraud โ Deliveries with missing or incorrect items can lead to unaccounted losses.
- Damage and Spoilage โ Broken, expired, or defective goods must be removed from inventory but may not always be properly recorded.
- Misplaced or Lost Inventory โ Poor warehouse organization can lead to misplaced items that are mistakenly recorded as shrinkage.
- Mispicks โ Errors in ecommerce order fulfillment may not be reported by customers, leading to inventory discrepancies.
Preventing shrinkage requires strong inventory management, accurate record-keeping, and security measures. However, partnering with a trusted fulfillment provider can play a critical role in minimizing shrinkage from issues like damage and mispicks.
Real-World Inventory Shrinkage
Hydrogenated water brand, HyVIDA, was seeing a great deal of inventory shrinkage in the form of products being damaged in transit. As a high-end brand committed to using only the highest-quality ingredients, they couldnโt afford to sustain the average of 1 to 4 cans of damaged product per shipment they were seeing. Ultimately, they found that by finding a new fulfillment provider that developed a customer packout procedure to protect their product, they were able to eliminate inventory shrinkage due to damage. Not only were their inventory costs improved, but their customer experience was greatly improved, leading to positive customer reviews and increased brand equity.
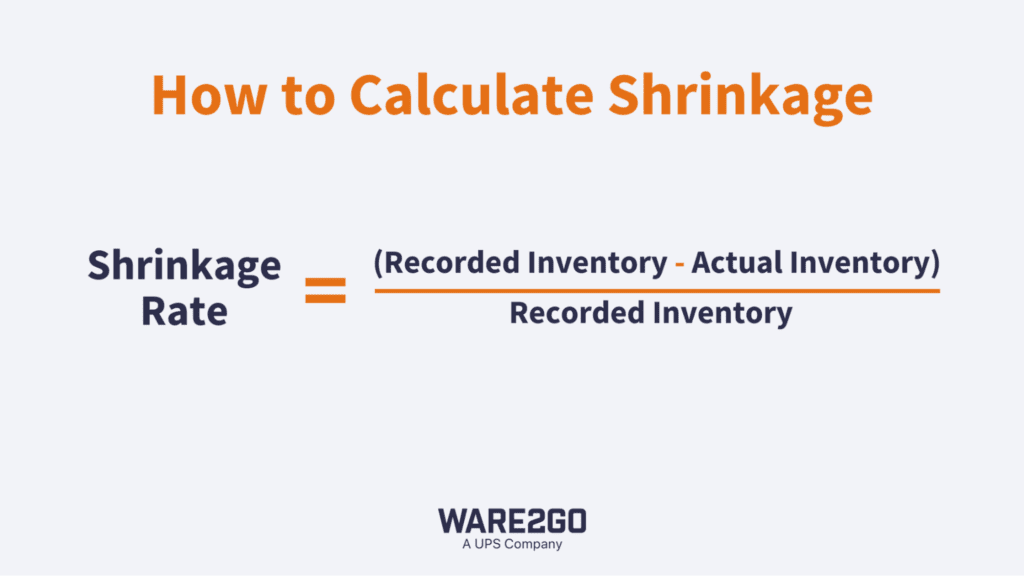
How to Calculate Your Inventory Shrinkage Rate
To calculate inventory shrinkage, use the formula:
Inventory Shrinkage Rate = ((Recorded Inventory – Actual Inventory) / Recorded Inventory) ร 100
This formula measures shrinkage as a percentage over a specific time frame, such as monthly, quarterly, or annually. Calculating shrinkage regularly helps businesses track trends and identify problem areas.
To determine the cost of inventory shrinkage, multiply the shrinkage rate by the total inventory value.
Cost of Shrinkage = Shrinkage Rate ร Total Inventory Value
Example:
If a company records $100,000 worth of inventory but only counts $95,000 in physical stock, the shrinkage rate is:
((100,000 – 95,000) / 100,000) ร 100 = 5%
If the total inventory value is $200,000, the cost of shrinkage is:
0.05 ร 200,000 = $10,000
This calculation helps businesses accurately quantify losses, identify problem areas, and implement targeted strategies to reduce shrinkage and protect profit margins.
Impacts of Inventory Shrinkage
Inventory shrinkage can have far-reaching consequences for businesses beyond just lost inventory. Understanding these impacts is essential for developing effective strategies to mitigate shrinkage and protect profitability.
- Financial Losses: Inventory shrinkage directly affects a companyโs bottom line. When inventory goes missing due to theft, damage, or administrative errors, it reduces the available stock for sale, leading to immediate profit losses. But the financial damage doesnโt stop there. Indirect costs, such as the expenses related to investigating discrepancies, implementing new tracking systems, and higher insurance premiums to account for increased risk, can further erode profitability.
- Operational Challenges: Inventory shrinkage also introduces significant operational challenges. When inventory counts are inaccurate, businesses may experience stockouts that result in lost sales and frustrated customers. The time spent tracking down discrepancies and reconciling records is time that could be better spent on more productive tasks. Additionally, shrinkage can cause inefficiencies throughout the supply chain, disrupting workflows and diminishing overall productivity.
- Poor Customer Experiences: For businesses that rely on accurate and timely order fulfillment, inventory shrinkage can seriously damage customer relationships. Stockouts, delayed fulfillment, or products lost during shipping can create negative customer experiences. Repeated errors or delays can lead to customer churn and reputational damage thatโs difficult to recover from, especially in a highly competitive market.
- Lower Employee Morale: Inventory shrinkage doesnโt just affect profits and operations; it also impacts company culture. When shrinkage occurs, companies often implement stricter control measures and oversight, which can create an atmosphere of distrust. Honest employees may feel unfairly scrutinized or demotivated by added layers of control, resulting in reduced productivity and engagement. Addressing shrinkage effectively requires a balanced approach that targets the root causes without alienating employees.
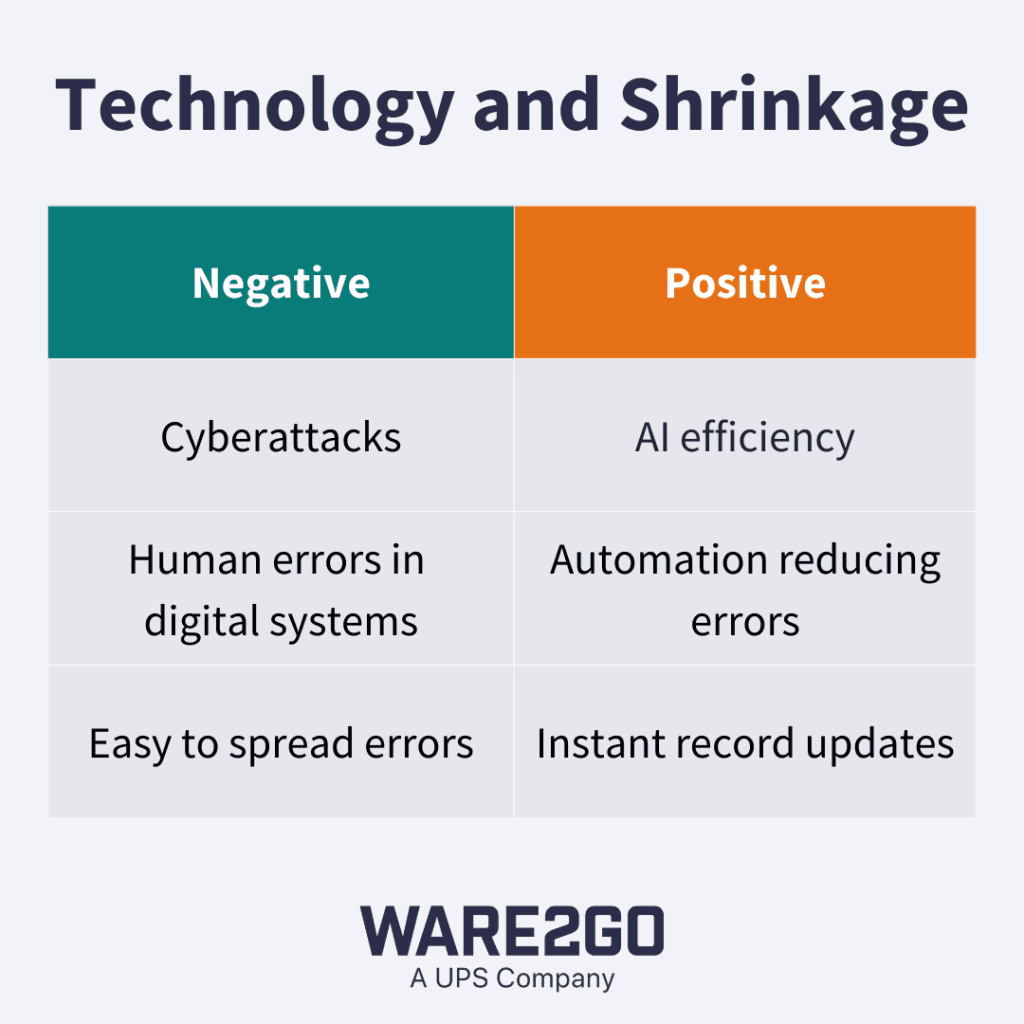
How Technology Is Solving โ and Causing โ Inventory Shrinkage
โInventory shrinkage poses significant challenges for retailers, with losses reaching approximately $100 billion annually. โ
While inventory management has evolved beyond handwritten records and phone calls to warehouses, many processes remain fragmented. Digital spreadsheets can be misplaced in email inboxes or desktop folders as easily as physical documents can be lost in filing cabinets or discarded. Accounting errors can occur with a keystroke just as quickly as with the flick of a pen. Historically, “paper shrink” caused by human error accounted for a significant portion of inventory shrinkage.โ
Additionally, top causes of inventory shrinkage, such as theft and fraud, continue to concern merchants, while the emergence of cyberattacks introduces new threats.โ
To combat these issues, businesses are increasingly turning to automation, machine learning, and data analytics. These technologies enable retailers to identify unusual activity, catch administrative errors, dynamically adjust pricing, and mitigate losses associated with shrinkage. โ
Small and medium-sized businesses (SMBs) can leverage their agility to adopt these advanced solutions, addressing both longstanding and emerging challenges in inventory management.
6 Tips For Protecting Your Inventory And Reducing Inventory Shrinkage Immediately
1. Ask for data-back service level agreements (SLAs)
SMBs often donโt get their fair shake when it comes to service level agreements (SLAs). Larger retailers can use their influence to dominate space on warehouse shelves, but an inventory management system that uses big data and double-verification creates 99.5% cycle count accuracy. Not only does this reduce inventory shrinkage, it also creates accountability and a true partnership between merchants and 3PLs and 4PLs.
When negotiating an SLA, make sure the terms are based on data like Average Daily Volume (ADV) and cycle count accuracy. If, like HyVIDA, you have a product that is easily damaged in transit, negotiate custom packout SOPs that will guarantee the safe delivery of your product and eliminate inventory shrinkage due to damages.
Learn how Ware2Go negotiates top-tier SLAs for merchants of all sizes
2. Create a streamlined vertical by integrating systems
Patchworking together different technologies for every facet of warehousing and distribution can lead to inventory shrinkage. Just like physically losing inventory in the supply chain, data can also be lost, and managing a disconnected suite of systems adds a layer of workโtime that could be spent on optimizing business. By combining a Warehouse Management System (WMS), Order Management System (OMS), and Transportation Management System (TMS) into one platform, merchants are able to accomplish seamless fulfillment management.
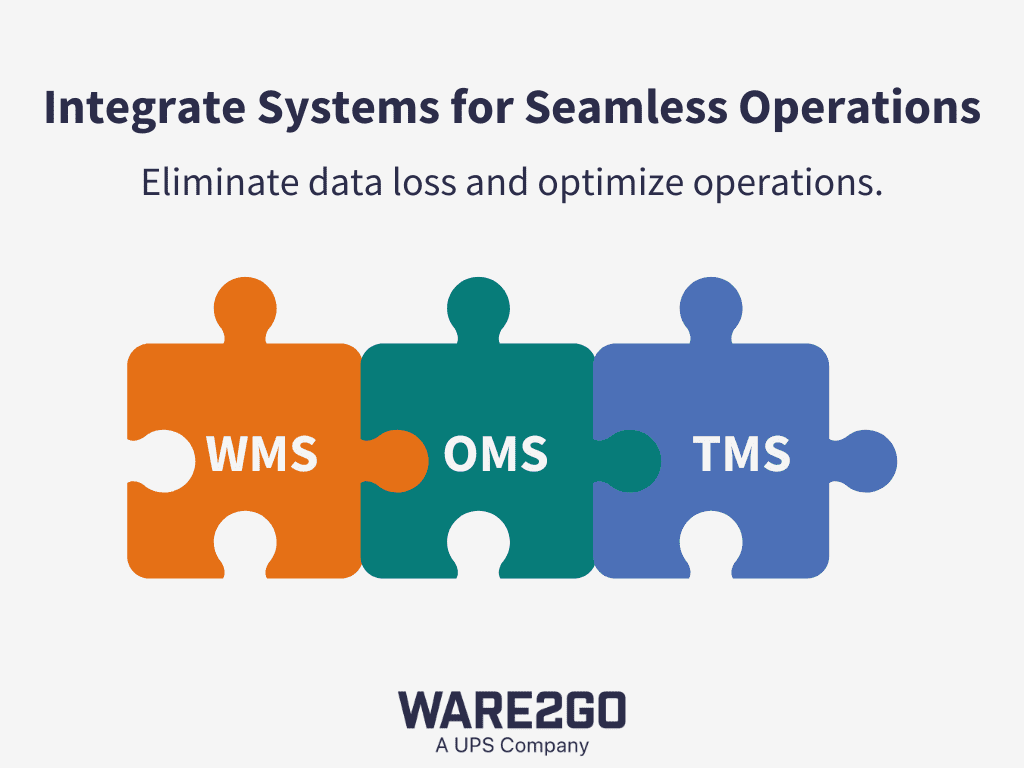
3. Automate time-consuming, detail-oriented tasks
Fulfillment workflow comes down to details that can reduce or increase inventory shrinkage. However, Warehouse Management Systems often put the onus of those details on merchantsโbut with smart technology, more inventory and demand for products doesnโt mean more work. By automating key touchpoints in fulfillment processes like order management, delivery tracking, and inventory management, merchants can ensure a more reliable fulfillment workflow and reduce inventory shrinkage.
4. Choose technology thatโs as nimble as your business
For SMBs, flexibility is critical. Change happens, and when it does, merchants shouldnโt have to worry about their inventory or workflow being in jeopardy. No matter who your ecommerce fulfillment provider is or how your tech stack may change, the right inventory management system should be able to adapt with it, whether directly on a dashboard or running in the background.
5. Shift to on-demand, holistic reporting
An accurate inventory count should be readily available at your fingertips. While automation and big data solve for fulfillment workflow optimization, being able to visually show success to team members and other internal stakeholders is critical in decision-making and executive buy-in. The right Warehouse Management System should allow merchants to monitor inventory, check fulfillment statuses, and access tracking information without any manual number crunching or having to make sense of isolated data sets from separate reports.
6. Make inventory shrinkage a measurable KPI
While some inventory shrinkage is inevitable for every merchant, that doesnโt mean it has to go unchecked. Ask yourself: Do I know what my inventory shrink rate is today? If youโre like many merchants in the US, inventory shrinkage may be a growing problem. With automation to safeguard against common causes of โpaper shrinkโ and inventory shrinkage, merchants can win back time to optimize other critical parts of their business without having to worry about their fulfillment workflow or being on the wrong side of shrinkage statistics.
Want to learn more about emerging trends for reducing inventory shrinkage and other industry best practices? Review some of the latest market research on Warehousing & Fulfillment or see real world examples of how warehousing is changing through the power of data, automation, and holistic management backed by smart technology.
Start Mitigating Shrinkage Today
Protecting your inventory from shrinkage doesnโt have to be overwhelming or unattainable. With the right strategies โ like using new technology, streamlining systems, and negotiating data-backed SLAs โ you can safeguard your bottom line and improve operational efficiency.
By working with a fulfillment provider like Ware2Go, equipped with innovative tools and data-driven insights, you can take proactive steps to minimize inventory shrinkage and optimize your supply chain. Ready to reduce inventory shrinkage and protect your business? Connect with our team of experts to get started today.