Logistics is a constantly changing industry with a sea of choices.ย
You’re in good company if youโre deciding between third-party logistics (3PL) and fourth-party logistics (4PL) services.
Understanding the difference between 3PL and 4PL is one of the most important steps to finding the perfect outsourced logistics partner. A 3PL company works best when looking for help with certain aspects of your shipping, while 4PL services are best suited when you require holistic solutions.
It depends on what services you need.
Are you searching for the most efficient way to meet customer expectations for fast shipping? Do you want to reduce shipping costs to where most customers are located?
Finding the right fulfillment partner will help you grow your business on your terms.
This guide is a head-to-head comparison of 3PL and 4PL to help you determine which path will lead you to smoother operations and happier customers.
Understanding 3PL vs 4PL
Third-party logistics (3PL) and Fourth-party logistics (4PL) are often used interchangeably.
While these two services may seem very similar on the surface โ both offer a similarly wide range of services, from packaging to warehousing and transportation โ there are major differences in their storage capacity, operational scalability, and technology.
What Is a 3PL?
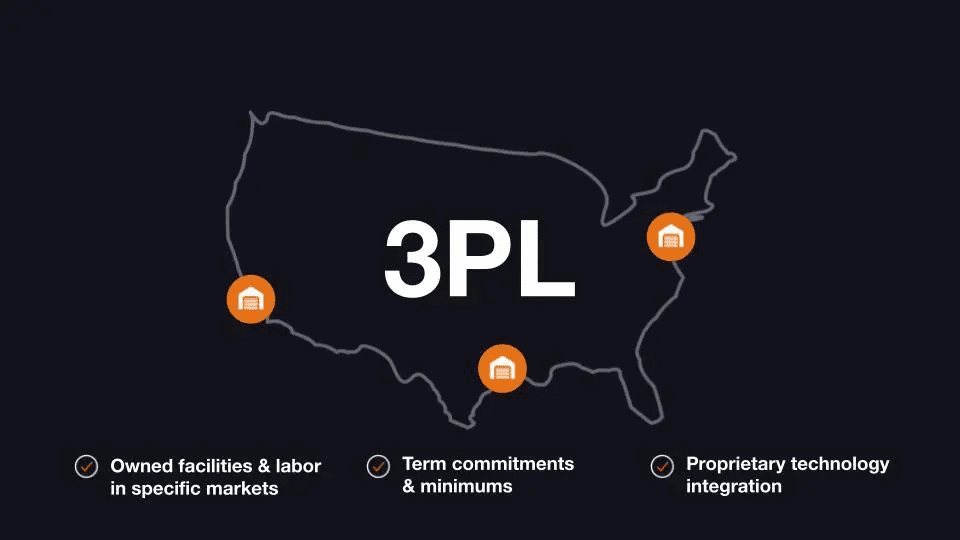
A 3PL (third-party logistics) provider is an outsourced fulfillment solution providing warehousing, pick, pack, and ship services.
The 3PL is a tried-and-true business model with the largest market share in the fulfillment industry, with a $280.9 billion valuation in 2023 and projected to clock over $400 billion in 2030.
3PLs usually have the following characteristics:
- Asset-heavy โ 3PLs typically own their facilities, labor, and warehouse management systems, making them reliable.
- Regional coverage โ Because 3PLs operate only with their facilities, they can only offer ground delivery coverage in their respective markets.
- Long-term commitments โ 3PLs often look for long-term commitments and may require an average daily volume (ADV) and storage commitment.
The primary benefit of outsourcing fulfillment to a 3PL is reduced overhead and strain on internal resources.
What Is a 4PL?
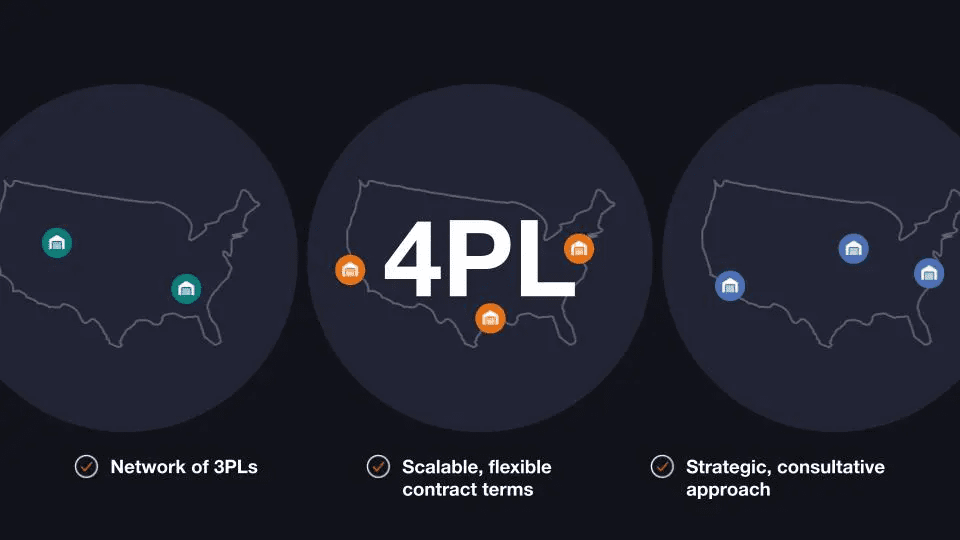
A 4PL (fourth-party logistics) provider is a network of multiple 3PLs connected through a single technology platform. 4PLs have a nationwide footprint to enable 1- to 2-day ground delivery across the US. Partnering with a 4PL can enable a small to mid-sized merchant to offer the same delivery promises as major retailers without sacrificing margins.
A 4PL is a strategic partner and negotiates the best rates and SLAs across the 3PL network. Using historical sales and shipping data, 4PLs advise merchants where to forward stock inventory to serve their customers best. 4PLs aggregate the inventory and shipping volumes of multiple merchants to negotiate the best SLAs and eliminate peak season surcharges.
3PL vs 4PL: Key Differences
According to McKinsey, traditional 3PLs struggle to keep up with the pace of eCommerce growth. eCommerce fulfillment requires speed, flexibility, diverse warehousing capabilities, and reverse logistics capabilities.
Generally, 4PL capabilities are more advanced and flexible than a traditional 3PL. The key differentiators of a 4PL include:
Storage Capacity & Delivery Footprint
3PL services are a portion of what a 4PL provides. Most 4PLs have a variety of warehouses and 3PLs in their network. They can provide more diverse shipping and storage capabilities and better geographical coverage. For instance, a 4PL network may contain warehouses specializing in big and bulky storage, lot tracking, and Seller Fulfilled Prime โ all within a single network.
Financial & Operational Scalability
With โon-demandโ 4PLs, merchants pay for only the resources they need when needed. They offer flexible contracts and service agreements, making them a highly scalable solution. 3PLs often require long-term contracts with stricter parameters around average daily order volumes.
Integrated Technology
4PLs typically operate through a cloud-based warehouse management solution (WMS), giving merchants visibility into order receiving, fulfillment, and delivery statuses across all facilities. A WMS should also integrate with eCommerce platforms like Shopify or WooCommerce and ERPs like Oracle or SAP for automated reporting.
3PL services need many parts to work together, which can take time and increase costs because you have to set up technology integrations manually.
On the other hand, 4PL services are easier to start using quickly because they’re designed to launch quickly. They typically offer instant, plug-and-play solutions that streamline the process.
Professional Support
Todayโs leading 4PLs will offer customer service beyond basic support. They offer strategic advice to merchants around inventorying, distribution, and management. Alternatively, traditional 3PL can only respond to basic inquiries and address day-to-day operational issues.
3PL vs 4PL: Key Process Differences
The key difference in the processes of 3PL and 4PL lies in the level of involvement and scope of responsibility each type of provider undertakes.
Hereโs a comparison of their operational models.
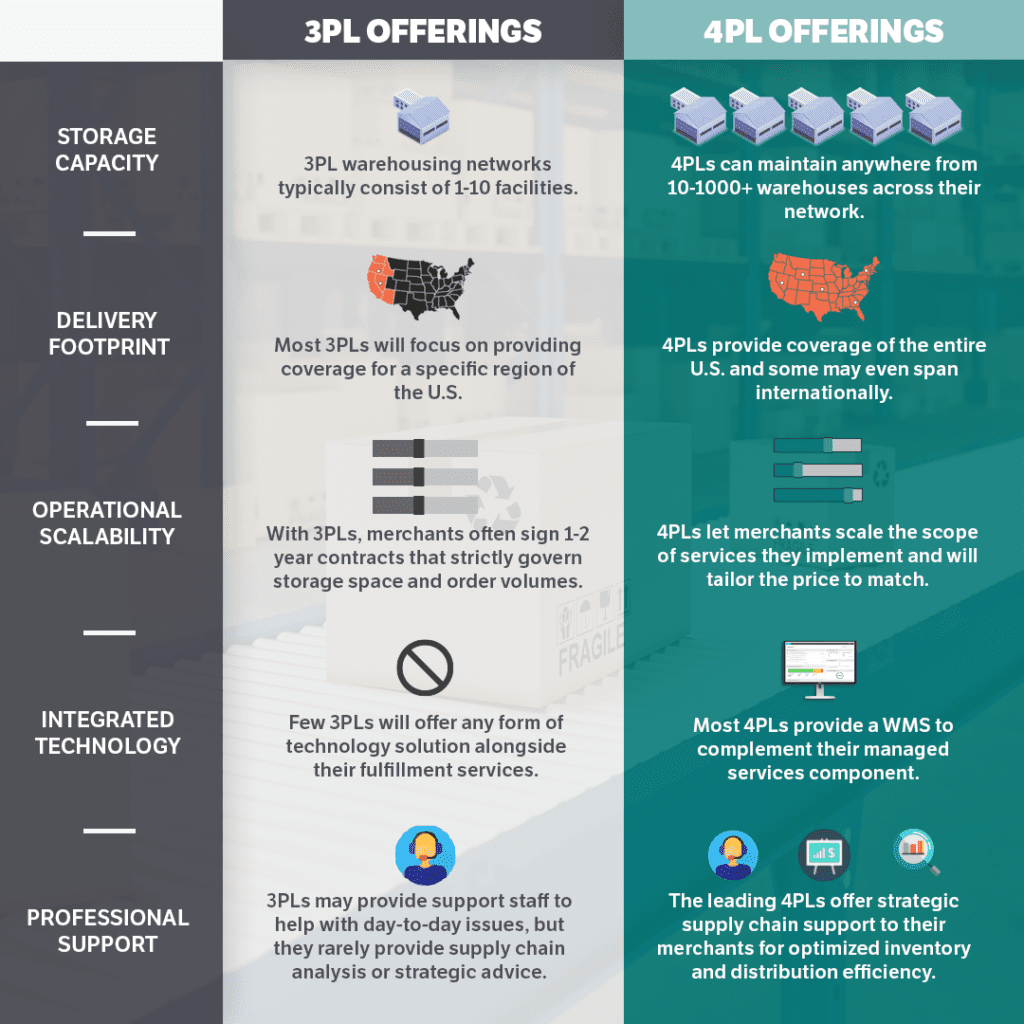
3PL Process
With 3PL logistics, you can hand over specific aspects of your logistics strategy to your provider, from warehousing to transportation and distribution.
You could send your products to the 3PL’s warehouse, and they take care of storing, picking, packing, and shipping orders to your customers.
They can also handle returns and warranty claims and integrate your business with their software ecosystems, including inventory and order management systems. Essentially, you’re delegating specific tasks to the 3PL but retaining control over the logistics strategy and decision-making.
For example, when a customer places an order on your website, the 3PL selects the items from the warehouse, packs them securely, and ships them out for delivery.
3PL services offer experienced professionals who know their job well, leading to smoother and faster deliveries for your business. They use special technology and methods to reduce mistakes and lower product shipping risks.
4PL Process
With 4PL logistics, you’re partnering with a provider that can manage your entire supply chain.
They coordinate with various 3PLs to ensure all your logistics, from warehousing to the final mile delivery, are optimized. A 4PL provider will oversee your products’ storage, handling, transportation, and distribution, ensuring everything runs smoothly from start to finish.
For example, a 4PL provider combines shipping and storage services into one efficient system. They use advanced software to track your products and ensure everything is delivered on time.
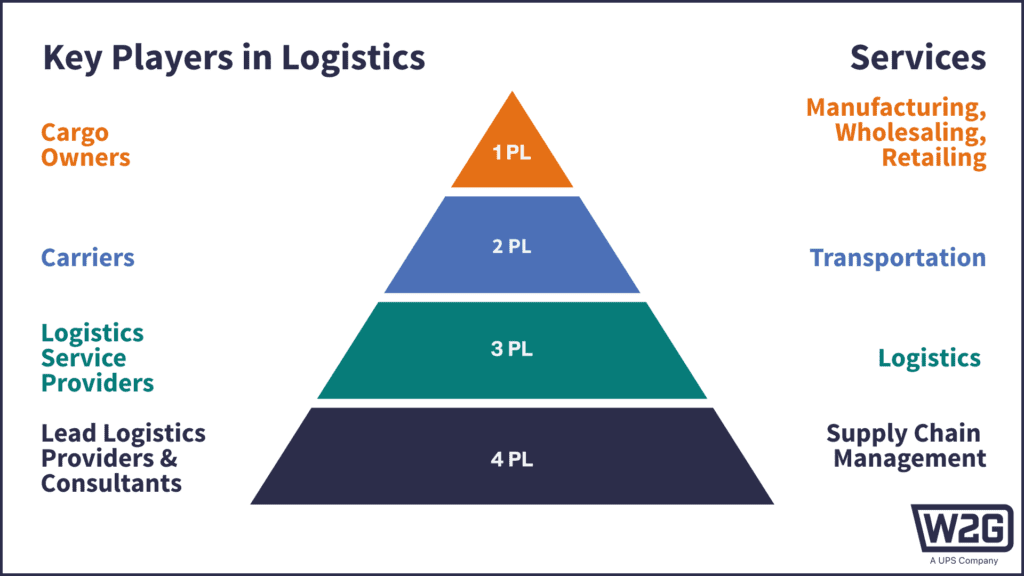
Collaborative Logistics: Synergizing 3PL and 4PL
Collaborative logistics combines the strengths of 3PL and 4PL to enhance supply chain management. This approach allows for better control of your logistics operations, covering detailed tasks and overall strategy.
Imagine a scenario where a 3PL handles the day-to-day operations like warehousing, transportation, and order fulfillment. At the same time, a 4PL coordinates these activities, optimizes routes, and utilizes data analytics to drive effective decision-making.
Combining the operational expertise of 3PLs with the holistic coordination of 4PLs can lead to unparalleled efficiency, flexibility, and responsiveness in their logistics operations.
Collaborative logistics can offer streamlined processes, reduced costs, supply chain agility, and resilience. It’s a winning formula that many businesses use in today’s competitive marketplace โ and the reason why growth in the 3PL and 4PL industries seems to go hand-in-hand, as seen in the graph above.
5 Questions to Ask When Selecting an Outsourced Logistics Provider
Business is global, which means companies need to think bigger about how they manage their products from start to finish. Big trends and smart strategies are important right now in logistics.
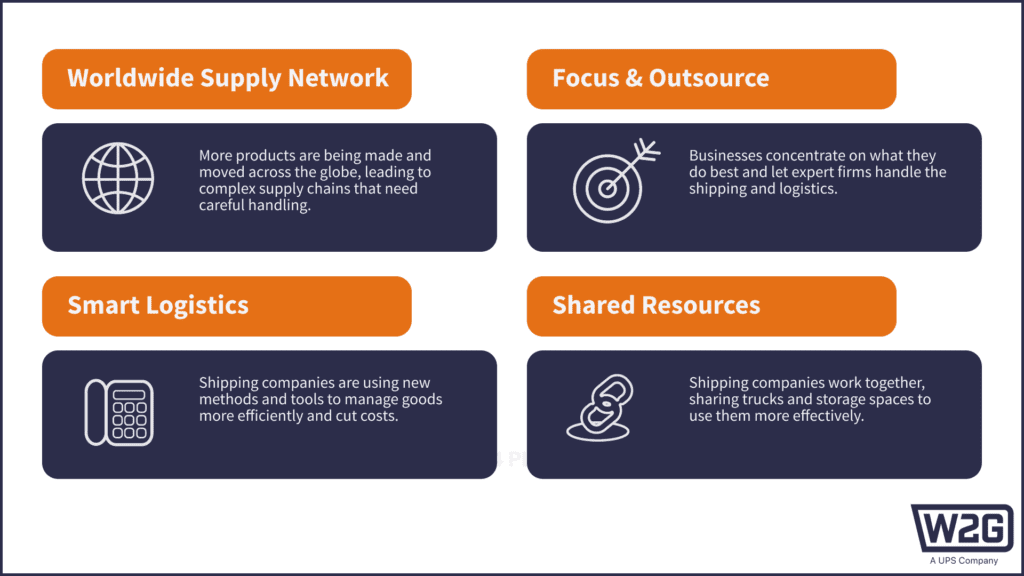
Whether you pick a 3PL for your business or opt for 4PL advantages, itโs important to vet all potential outsourced fulfillment partners depending on your needs.
Below are 5 questions that will help you find the ideal fulfillment partner.
1. Can They Handle Your Warehousing and Fulfillment Needs?
Do you have perishable or frail items needing special handling and storage? How much storage space will you need, and how will volume shift with seasonal demands? โ
2. Can You Reach Your Customers Quickly?
It is important to understand each warehouseโs geographic coverage and shipping methods. For instance, you may need a partner that can reach all customers with two-day shipping at ground shipping rates. Amazon sellers, in particular, should look for a 4PL logistics provider capable of meeting Seller Fulfilled Prime (SFP), Fulfilled by Merchant (FBM), and Fulfillment by Amazon (FBA) prep requirements.
3. How Will Your Fulfillment Costs or Overall Customer Acquisition Costs be Affected?
Understandably, most small to mid-sized merchants are looking first and foremost to lower their customer acquisition costs. Data increasingly shows that advertising a 1 to 2-day delivery promise at the top of the sales funnel increases conversions and overall market share.
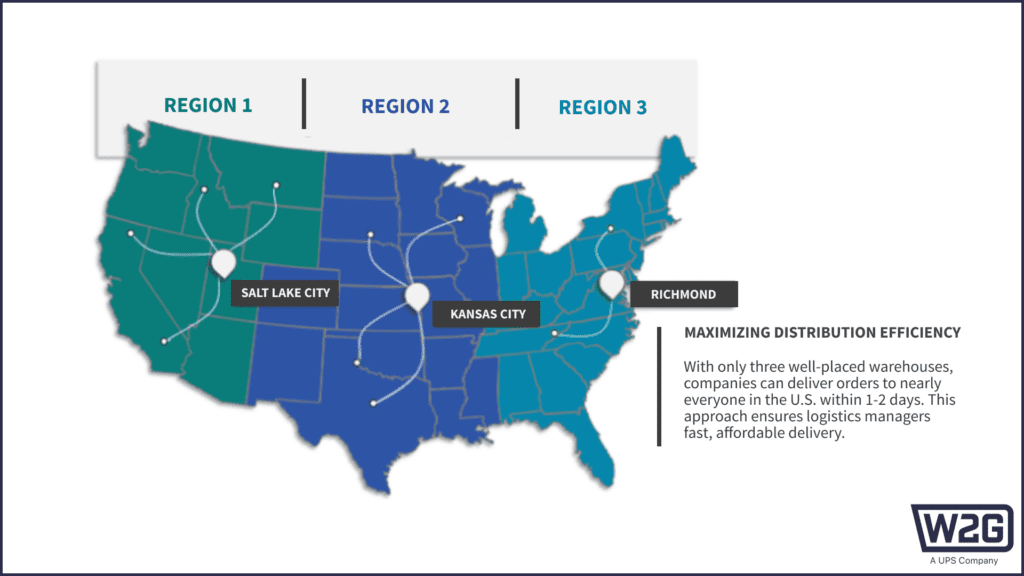
Look for providers who understand these kinds of insights, and consider the relationship between top-line revenue and bottom-line profitability when comparing cost.
4. What Level of Warehouse and Customer Support Can You Expect?
The trade-off to outsourcing your fulfillment is often visibility and control. Therefore, itโs vital to have a strong understanding of what your partnerโs client support will provide to you. Dig in and ask questions about on-time fulfillment speeds, complaint resolution speeds, dock-to-stock time, and security measures to understand their warehousing processes and service levels. And donโt be afraid to ask for a reference from an active client before signing a contract.
5. Are Technology and Integrations a Priority?
Integrated technology bridges the gap between delivery (where sales and operations meet) and every other part of the business. It allows a full-funnel view of the supply chain and the sales cycle for a more accurate calculation of customer acquisition costs (CAC) and overall cost.
Most merchants see the tremendous value in plugging their order management systems, marketplace sales channels, and ERP systems into their WMS. Additionally, the WMS will provide daily reporting on order status, inventory levels, and fulfillment status.
5 KPIs to Benchmark Success with 3PL and 4PL
Benchmarking success with 3PL and 4PL companies is essential for evaluating performance and driving continuous improvement in logistics operations.
Here are five key performance indicators (KPIs) to consider:
1. On-Time Delivery Performance
Measure the percentage of orders delivered to customers within a specified timeframe. Timely deliveries are vital for customer satisfaction and retention.
2. Inventory Turnover Ratio
Calculate how efficiently inventory is sold and replenished within a given period. A higher turnover ratio indicates optimal inventory management and minimized holding costs.
3. Order Accuracy
Evaluate the percentage of orders fulfilled accurately without errors or discrepancies. High-order accuracy signifies operational excellence and enhances customer trust.
4. Cost Per Order
Analyze the total cost incurred per order fulfilled, including transportation, warehousing, and handling expenses. Find ways to lower your cost per order to improve your profitability. Consider economies of scale that may come from multi-pick orders and larger cart sizes.
5. Customer Satisfaction Score (CSAT)
Measure customer satisfaction through surveys or feedback to assess the overall experience with logistics services. A high CSAT score reflects positive customer perceptions and reinforces loyalty to the brand.
By keeping track of these key performance indicators (KPIs), companies can evaluate how well their third-party (3PL) and fourth-party (4PL) logistics providers are doing. This helps them adjust their logistics plans to match their business goals better, making them more competitive.
3PL vs 4PL Is Only the Beginning: 1PL to 8PL and Beyond
Choosing the right logistics service, like 3PL or 4PL, is important now, but what about the future?

Letโs explore what comes next in logistics to prepare you for upcoming changes:
1PL โ This is where companies do everything for themselves โ from storing to delivering products. Itโs good for small operations but might not keep up as your business grows.
2PL โ At this stage, businesses start outsourcing by using external services for transport and storage, helping them handle more work.
3PL and 4PL โ Youโre likely familiar with these. 3PL helps with specific tasks like shipping and storing, while 4PL manages the entire logistics process, offering a bigger-picture solution.
5PL โ This model uses smart technology, like AI, to make the supply chain more efficient, saving time and money while providing valuable insights for better decision-making.
6PL โ Here, the focus is on being eco-friendly, helping businesses reduce their environmental impact, and appealing to customers who value sustainability.
7PL โ Imagines managing global logistics, making it easier for businesses to operate worldwide with seamless coordination.
8PL โ Looks forward to fully automated logistics, where technology takes over to streamline operations and potentially reduce errors and costs.
Understanding these stages helps you think ahead and prepare your business for the future of logistics. While the choice is currently between 3PL and 4PL, knowing about 5PL to 8PL gives you a glimpse into how you can grow and evolve in logistics.
3PL vs 4PL: Charting Your Course to Growth and Success
As eCommerce evolves, shoppers increasingly expect a faster, cheaper, and more transparent shopping experience. Many brands, therefore, are looking for partnerships that enable a headless supply chain for ultimate flexibility. These types of partnerships are:
- WMS-agnostic, allowing merchants to add any warehouse to their network, including their facilities.
- Employ technology that connects end-to-end commerce operations, from supply chain to sales and marketing.
- Offer full-service supply chain solutions from the factory floor to the front door.
- Rely on predictive analytics for robust demand forecasting and inventory optimizations.
- Include advanced order orchestration for smarter order routing.
Scale your business on your own terms with our fulfillment solutions. Get in touch with us today to register or for more information.